The Essential Guide to 3D Printing Carbon Fiber filled Nylon
- alexespinosa5
- Jul 18, 2022
- 5 min read
Updated: Jul 20, 2022

You've probably heard that 3D printing carbon fiber-filled nylon is difficult. You may have heard it requires special hardware. Well that's half true. You will need a few essential components to be successful at it, but it's not that difficult. And this filament is worth the effort. Nylon is tough and has excellent layer adhesion. The addition of carbon fiber (CF) to the filament makes it stiffer and reduces the material's tendency to shrink during cooling. This means you can print it at room temperature and get amazing prints. The finished parts are strong, tough, and temperature resistant! Here are a few tips that will ensure success.
If at first you don't succeed, DRY DRY DRY!
This may as well be the title of the blog post. I can't emphasize enough how important this is. Nylon is hygroscopic, meaning that it readily absorbs moisture from the air. When printing, this moisture turns to steam and expands inside the filament as it's extruded. This causes several issues including a rough surface, blobs, and stringing. So how do you ensure your filament is dry?
Dry in a convection oven at 90° C for 4+ hours
There are several filament dryers on the market. They range from re-branded food dehydrators to purpose-built devices. But these units have a limited temperature range. We dry our nylon filament in a convection oven with a tightly controlled PID temperature controller at 90 C for 4 to 8 hours. Weigh your spool first on a gram scale. Write the value on the spool before it goes into the oven and then repeat when it comes out. You may be surprised to see it lose several grams of water. Don't forget to dry your desiccant material at the same time and weigh it too. Understanding the weight loss will help you understand your drying process.
Dry that brand new spool too
Just because you opened up a fresh spool of filament doesn't mean you can skip this step. We typically extract about 10 grams of water from new 1Kg spools (that's 1% by weight!). The image below shows a part printed with two spools of carbon fiber filled nylon from the same brand. The lower part was printed with dried filament and the upper 2 mm with a spool of fresh filament straight out of a vacuum sealed bag. You can clearly see a color change and blobs of material on the upper 2mm of the part. The same spool lost 1% of moisture after drying.
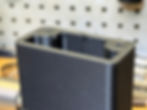
Print out of a dry box
This may seem overkill if you're used to printing the same spool of PLA for weeks with no conditioning. But nylon filament will absorb enough moisture to ruin your print if it lasts more than a couple of hours (not to mention needing to be dried again for your next print). The solution is to store and use the filament in a sealed, dry box.

The filament should exit the box through a tube that runs directly into the extruder to minimize moist air contact. What else should you keep in your dry box? Dried desiccant and a digital hydrometer. You can find hydrometers on Amazon and other online vendors. If the relative humidity rises above 10%, you should re-dry the filament and the desiccant. Please note that cheaper hydrometers don't display values below 10%. This is the range that you are most interested in.
Turn up the heat, Turn off the cooling fan
You know that nylon needs to be printed hotter than PLA or ABS. The exact temperature will vary by material and printer setup. We run between 280°C and 295°C. This will require an all-metal hotend.
Not all hotends are created equally
Now that your all-metal hotend can reach a searing 300°C, you may start to find new problems. One new thing to consider is the efficiency of the hotend's heat break. The heat break is the part between the hot nozzle, and the cold tube leading to it, usually surrounded by a heat sink. When the nozzle is running hotter, more heat will be transferred through the heat break, into the cold end of the hotened. If the filament melts in this zone, it will get stuck and be quite difficult to remove. You may want to add a bigger fan or better ducting to the heat sink (as I did). Instead, consider buying a better hotened that performs better at higher temperature.
Speaking of fans
You might think that printing at such high temperatures means you need to run the part cooling fan. But nylon does not need part cooling. In fact, you will lose layer adhesion strength if you do. Running the fan slowly over bridges only is acceptable, but leave it off for the print. If small islands are being printed, you can experiment with slowing down the print speed. You can then add minimal fan speed if needed. But for general printing, it should be off.
Should I buy a super-hard, diamond-tipped nozzle?
No. But you do need something harder than brass. The reason is that carbon fiber filled nylon will erode the nozzle. The carbon filler is abrasive and will destroy a brass nozzle in a short time. Hardened steel nozzles from quality vendors are an excellent alternative. But heat transfer through the steel into the filament is worse. Increase the print temperatures and slow down the maximum speeds a bit when using steel. Another option would be to use a ruby-tipped brass nozzle. You'd get the heat transfer of the brass, and the abrasion resistance of a ruby.

What about build surfaces, heated chambers, etc?
Build surface and adhesion
When it comes to build surface, the secret sauce is PVA glue or regular glue stick. PEX is a favorite build surface at Pilot Line but garolite works well too. Either surface has to be coated with glue stick. The first layer parameters must also be correct (speed, height, etc).
Chamber Temperature
For chamber temperature, you're in luck. Carbon fiber filled nylon doesn't require a heated chamber. Room temperature or higher will work well. The carbon fiber helps reduce shrinking and warping in the nylon which helps stabilize it.
Build plate Temperature
The build surface does not have to be heated. We run a PEX build surface at 45°C out of tradition. Markforged printers do very well with an unheated garolite bed (and glue stick).
Print settings
Are you wondering how much retraction nylon needs to avoid oozing and stringing? Scroll back up and read the section on drying the filament. Seriously, there are no special settings needed to print nylon. Of course you'll have to experiment with the usual print settings to see what works best. If you find yourself running twice the normal retraction to avoid oozing, the problem is moisture in the filament. Dry it and try again.
Why are my nylon parts getting softer over time?
Remember that nylon is hygroscopic? Well your super-dry freshly 3D printed part is now absorbing moisture from the air. This moisture acts as a plasticizer. A plasticizer is something that is added to a thermoplastic to make it softer. This softening of the material after it's exposed to real-world conditions is something that must be considered when designing a nylon part. If you need a very stiff part, try PLA. If you want something amazingly tough with some decent stiffness that can take some heat, it's hard to beat CF nylon.
I hope this guide helps clarify the topic of 3D printing CF filled nylon. It might be your new favorite filament. Let us know what your experience is like, or if you have other tips for printing nylon. Good luck!